Trans-humeral Prosthetic System
(Patent Application in Progress)
A low-cost, 3D-printed elbow and trans-humeral socket for amputees in developing countries
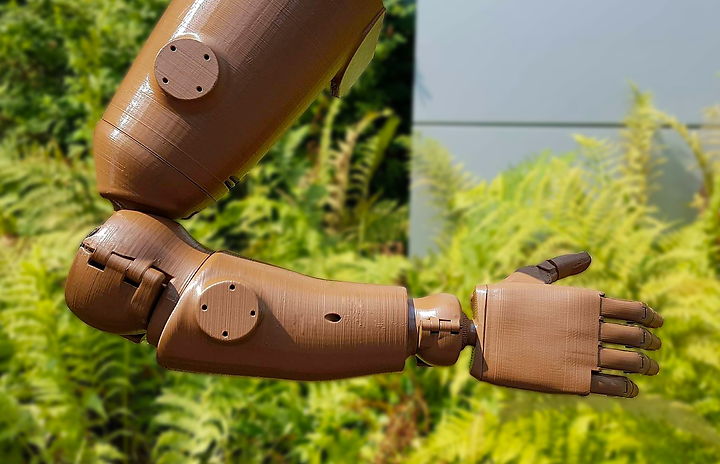
The Problem
The existing 3D-printed Victoria Hand system would only work on trans-radial amputees.
The Design
After conducting background research, design constraints and objectives were identified and two designs for elbow joint mechanisms to be used in a transhumeral 3D-printed prosthetic system were developed. Both systems were then evaluated both quantitatively and qualitatively.
Objectives
-
Functional range of motion
-
Low cost
-
Low/anatomically correct weight
-
Device is robust
-
Device is easy to use with one hand
​
​
​
Constraints
-
Majority of the prosthetic must be 3D-printed
-
Material must be 2.85mm EasyFil PLA
-
Type of 3D-printer must be an Ultimaker 2+
-
Prosthetic must achieve at least 110 degrees flexion
​
Concept 1 - Side Button

Entire Side Button system with 145 degrees flexion shown
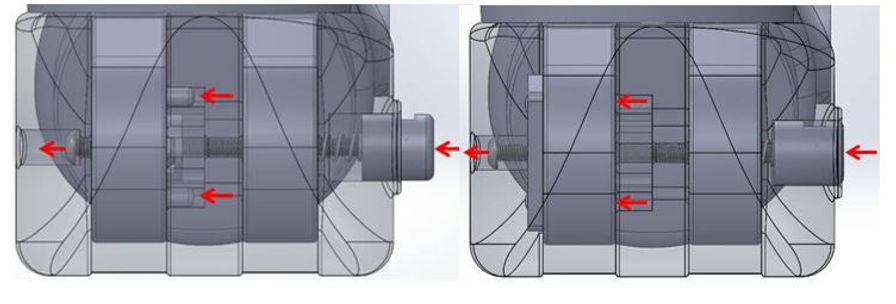
The first concept incorporates a push-spring system to lock and unlock the elbow at 5 different angles between 0 and 145 degrees.
​
The internal mechanism can be seen in the two figures below. When the button is pushed, the 5mm pins will disengage from their locking position allowing the arm to be rotated to another pin slot. When the arm is in the desired slot, the spring will push the button out again and lock the arm in place.
​
​
​
Side button internal mechanism locked (left) and unlocked (right)
Concept 2 - Ball and Socket
The current VHP prosthetic wrist utilizes a ball and socket system that can be rotated 360 degrees and flex and extend 25 degrees to each side and locked as shown below.
​
​
​


Side button internal mechanism locked (left) and unlocked (right)
This concept was adapted to work effectively as an elbow. Notches were cut to increase the amount of rotation and changes were made to the mechanism to increase the locking force. To accurately resemble the planar motion of an elbow, one side of the inner ball was made flat. Additionally, the socket is designed to fit snugly to the ball when unlocked. This allows for easy rotation of the forearm but holds the forearm tightly enough that the user can let go of it and lock the joint without its position shifting.The full system can be seen below.
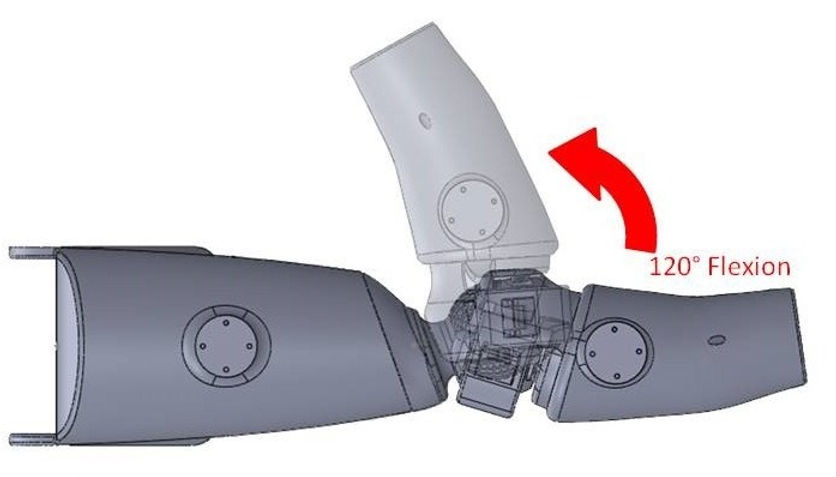
Entire ball and socket system with 120 degrees flexion shown
Concept Comparative Evaluation
The ball and socket concept achieved a degree of rotation of 120 degrees which was 10 degrees less than that of the side button which had 145 degrees. Both concepts surpassed the design goal to rotate at least 110 degrees.
The material cost of the side button concept was $13.82 and the ball and socket concept was $11.49. Both concepts met and surpassed the design goal to cost less than $30.
​
A 3D-printing software called Cura and the specifications sheet for each non-3D-printed part, were used to estimate the weight of each concept. The side button and ball and socket's respective weights were 0.97lbs and 0.58lbs.
​
The ball and socket was able to be locked in a far greater number of positions (unlimited) than the side button (five). Both concepts were easy to rotate into the desired angle using just one hand.
For more information about the Victoria Hand Project (VHP):