VC200 Prosthetic Hand
A low-cost, 3D-printed prosthetic hand for amputees in low-income countries
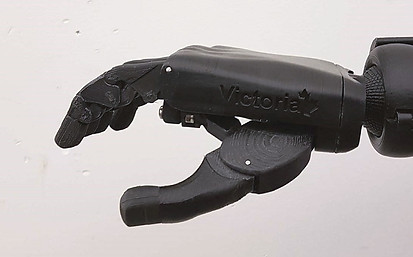

The Problem
The existing 3D-printed, VC186 Victoria Hand was outdated. Based on client feedback, improvements were required in the hand aesthetics, cost, grip strength and ease of assembly.
The Design
After communicating with users of the VC186 hand, we determined the needs of an average user and identified constraints and objectives that had to be met during the improvement process.
Objectives
-
Improved grip strength
-
Low cost
-
Device is robust
-
Device is easy to assemble
-
Improved resemblance to a true hand
​
​
​
Constraints
-
Majority of the prosthetic must be 3D-printed
-
Material must be 2.85mm EasyFil PLA
-
Type of 3D-printer must be an Ultimaker 2+
-
Prosthetic hand must be actuated using one pull cable and incorporate existing adaptive grasp plate system.
​
Grip Strength
Although the grip strength of the VC186 prosthetic hand was satisfactory for everyday tasks, many users identified a need for a stronger grasp. The Victoria Hand is actuated through movement of the user’s shoulders which pulls a cable attached between the harness and the hand. A stronger, more efficient grasp allows the user to pick up heavier objects using less force from their shoulders, resulting in more comfortable use.
​
To address this need, two options were considered and implemented. Firstly, the number of parts in the finger assembly was reduced from six to just four. This change reduces the number of pins and rotational axes in the finger where substantial amounts of friction occur. This also increases work transfer efficiency by reducing side to side motion of the fingers where work is lost.
​
Secondly, overall tolerances and clearances in the hand were tested and standardised. When working at the micron level, 3D-printing is inaccurate. Multiple test samples were printed using four different 3D-printers. The results were compared and the optimal clearance and tight hole sizes as well as sliding clearances were identified.
​
​

Reduced Cost
VHP have designed a low-cost prosthesis using 3D-printing and laser scanning to replace complex machining and manufacturing processes.
​
By keeping as many materials and components of the design consistent with those used in other parts of the prosthesis system (wrist, socket, harness), costs associated with sourcing new components and shipping to partner countries can be avoided. Additionally, because of the limited empirical data associated with 3D-printing parts, utilising a proven method involving a specific material type and print settings will minimize issues such as print failure, layer separation and clogged nozzles.
​
To reduce the cost of the VC200 when compared with VC186, the number of required 3D-printed parts were decreased. This reduced the amount of polylactic acid (PLA) filament used per hand. Additionally, by removing parts such as the 5/8” screws that are not used anywhere else in the VHP system, shipping costs associated with sourcing parts were reduced.
​
​
Increased Durability
Considering sustainability, cost-effectiveness and functionality, it was important that the device could cope with the loads applied to it without slipping or breaking. 3D-printed parts will almost always break between the print layers. For this reason, the print orientation of each part must be considered to minimize stress along these layers.
​
In the VC186, a common issue was that the silicon fingertips would tear or rip. To address this issue, a more durable fingertip material had to be identified. It was determined that using a flexible, 3D-printable plastic would create much more durable fingertips but at a cost of decreased grip. To improve the grip, ‘pockets’, were incorporated into the fingertip design.
​
Through our clients’ feedback, it was also noted that the most common breakage was in the finger assemblies. To improve the strength of the fingers, the number of joints was reduced from three to two. Additionally, the wall thickness of the fingers was increased.
​
​
​
​
Improved Aesthetics
One of the biggest areas of improvement identified was to improve the resemblance of the prosthetic to that of an uninjured hand. To improve the resemblance, the hand had to become less box-like and the surfaces more curved. Additionally, obtrusive parts of the system needed to be streamlined.
​
Complex surfacing techniques were conducted using SolidWorks to create a palm and palm cover that were much smoother, smaller and life-like. Other components of the hand also had to be adapted to fit into the newly designed palm.
​
The coupler between the adaptive grasp plate and the thumb was obtrusive and would get in the way when users tried to grasp some objects. This mechanism was reduced in size and moved to the edge of the palm, instead of in between the index and middle-finger. No functionality was lost.
​
​

Easier Assembly
VHP distributes all of it’s Gcode print files to their print centers around the world where trained locals print and assemble the parts. For this reason, it is important that the assembly process be as simple and streamlined as possible. As the first, widely distributed Victoria Hand, the VC186 assembly process was lengthy.
In the VC186, the fingers would take the longest amount of time to assemble. By reducing the number of joints and parts in the fingers, the assembly time could be cut in half. It was also noted that parts with sharp inner corners were very difficult to sand. The new joints were designed so that files could easily access and sand the interior surfaces.
​
To reduce the amount of sanding required, the supports of the VC200 were optimized. Increasing the number of and standardizing the spacing between the supports results in a much smoother surface finish when the supports are removed. To standardize the support thickness and spacing, the limitations of the 3D-printer nozzle diameter as well as accuracy had to be considered and numerous tests were conducted.
One common complaint was associated with having to cut some of the 2mm steel dowel pins down to size. In the new VC200, new dowel pins were sourced so that they were all manufactured to the correct lengths required and did not require custom cutting.
​
Finally, the removal of the silicon fingertips reduced the overall hand assembly time by almost 20 hours. The silicon required mixing and then moulding onto the fingertips which would then be left to set for 24 hours. In comparison, the Flexifil can be attached, just like the PLA filament, to the 3D-printer which then takes approximately 3 hours to print a full set of fingertips. Additionally, once opened, the silicon would expire in just four months and require expensive shipping of a replacement. The Flexifil filament can last over a year.
​
​

Results
Qualitative and quantitative tests were conducted to evaluate the VC200 hand in comparison to the VC186. Index finger grip efficiency and tri-grip efficiency increased by 23% and 50% respectively. Material cost was reduced from $17.90 to $12.74 CAD. Assembly time was cut in half and the likeness to a true hand was greatly increased. Finger strength was also improved so that the VC200 could support more than 20N in comparison to the 12N limit of VC186.
​
Using a $250,000 grant received from Google.org, three-hundred VC200 hands are now being distributed to print centers and amputees in Guatemala, Ecuador, Haiti, Nepal, Cambodia and Egypt.
For more information about the Victoria Hand Project (VHP):
To read my blog post about VC200: